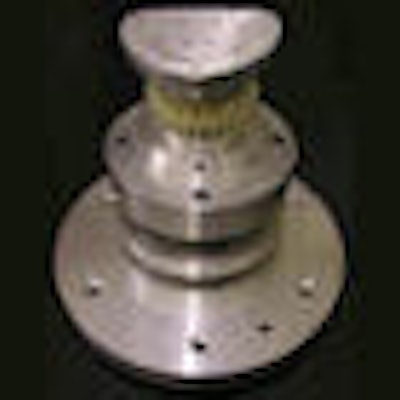
What qualities do you look for in a restoration? Comfort and attractiveness, of course. Biocompatibility, absolutely.
But first and foremost is wear and tear. You -- and your patients -- want those new and improved teeth to stand the test of time.
For years, developers of amalgams, composites, and ionomers have been challenged by the dental community's call for more durable materials that would last longer and be more attractive and easier to work with. But developing new dental materials takes time and money, requiring at least two to three years of randomized clinical trials and regulatory red tape before being close to market-ready.
This is where oral wear simulators come in. Since the 1980s, when the durability of dental materials was a more critical issue than it is today, laboratory simulators have been helping to accelerate the screening of materials wear and fatigue under controlled conditions. However, current laboratory wear simulators utilize only 2 to 3 degrees of freedom (DOF) and are unable to reflect true in vivo wear, which means the results from different simulators are often inconsistent.
A 2006 study comparing the Alabama, ACTA, OHSU, Zurich, and MTS simulators, for example, concluded that "As wear measurements in vivo are complicated and time-consuming, wear simulation devices and methods had been developed without ... systematically looking at the factors that influence important wear parameters" -- namely, force, force profile, contact time, sliding movement, and clearance of worn material (Dental Materials, August 2006, Vol. 22:8, pp. 712-734). "All wear methods lack the evidence of their clinical relevance because prospective studies correlating in vitro with long-term in vivo results with identical materials are not available," the study concluded.
"You need machines that can exert high forces and force control," Siegward Heintze, D.D.S., author of the 2006 Dental Materials study and head of in vitro research at Ivoclar Vivadent, told DrBicuspid.com. "Once you have that kind of machine, you can run the kinds of tests you need. But you also have to validate, and all of this takes time, which affects time to market. Time is a critical issue [in materials research]."
These issues are what prompted Kazem Alemzadeh, Ph.D., B.Sc., biomedical engineer and senior lecturer at the University of Bristol, to develop Dento-Munch, a computerized chewing simulator with two platforms that act as the upper and lower jaws. Like the human jaw, the lower jaw of Dento-Munch is capable of moving in 6-DOF: up and down, forward and backward, and left and right. In addition, feedback control software enables the robot actuators inside Dento-Munch to respond to loads meant to simulate the forces of muscle and tendon.
![]() |
Dento-Munch is a computerized chewing simulator with two platforms that function as the upper and lower jaws. Image courtesy of Kazem Alemzadeh, University of Bristol. |
Initial applications include systematic evaluation of wear and fatigue testing of restorative materials used in dental components such as individual teeth, crowns, bridges, and implants, Alemzadeh said. Potential customers include dental materials and component manufacturers such as Ormco, Nobel Biocare, Vita, Ivoclar, and Renishaw, he added.
But some dental materials experts say the need for sophisticated -- and potentially costly -- wear simulators such as the Dento-Munch has passed.
"Wear is not such a problem as it was in the past," said John Purk, D.D.S., M.S., Ph.D., head of operative dentistry in the department of restorative dentistry at the University of Missouri-Kansas City School of Dentistry.
Composite materials have become very wear-resistant, Dr. Heintze added, and the testing methods and mechanisms that are already used by companies like Ivoclar Vivadent are capable of accurately testing these materials.
"I am a bit skeptical [of the Dento-Munch]," he said. "It uses an existing platform that was developed decades ago, and Dr. Alemzadeh has made it very complex, which will be very costly." Researchers at Frankfurt University have been working to develop 3- and 4-DOF approaches and the materials cost alone was $20,000, he added.
Nevertheless, the existing platform is one of the most sophisticated control systems available at the present, Alemzadeh said, noting that it is currently being used in an aircraft simulator. He believes Dento-Munch -- and its 3D optical scanning system, Dental-OS, which he says can digitize a dental cast or impression faster than traditional mechanical or laser scanners -- bring a new level of sophistication to materials research. Dento-Munch's jaws can be loaded with personalized chewing patterns, which current simulators cannot do. In this way, the cause of failure of dental components can be related to individual occlusal loadings when wear pattern is analyzed. It also has many potential applications outside of dentistry, he added.
"The system could be used for food simulation, say by chewing gum manufacturers. Or by biscuit [cookie] manufacturers to determine how crunchy a biscuit is. The platform could also be used for ankle rehabilitation and physical modeling of spine injuries," he said. Dental-OS could also help orthodontists better determine where to place and attach braces, he added.
"We are in the process of developing a second generation of the jaws that will include the temperature and other oral conditions that exist in human jaws -- even create bacteria similar to what is on human teeth," Alemzadeh said. "This would make the whole device much more realistic."