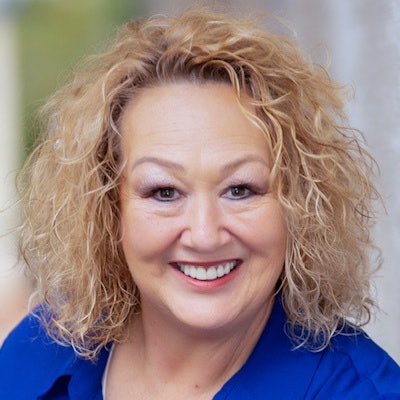
Dental office maintenance means more than cleaning equipment like autoclaves and ensuring they are used per manufacturers' instructions, according to a presenter at the Chicago Dental Society 2023 Midwinter Meeting.
Presenter Tija Hunter, a certified dental assistant and consultant in Illinois, said documenting when, how, and who took care of the equipment, as well as ensuring that more than one employee is trained on how to maintain them, are critical.
"Equipment is so expensive; I don't have to tell you that," Hunter said. "Regular maintenance will extend the life of the equipment for years!"
Handling equipment
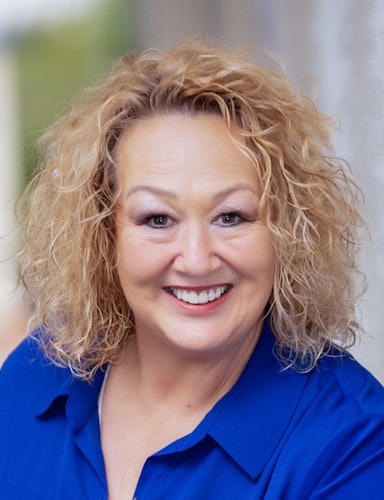
Though who is tasked with maintaining equipment often depends on time availability and the dynamics of a practice, every office should have a written protocol for each piece of equipment. The protocol guides the team as to when things need to be done and keeps staff members accountable for when they're done, Hunter explained.
There needs to be a protocol because each piece of equipment has a different service requirement. For example, Hunter services the practice's autoclave on the first of every month by cleaning it and performing the recommended maintenance. But O-rings and hoses should be done more frequently, she said.
Also, Hunter said that the dental team should pay close attention to what the manufacturer says about the use and maintenance of the equipment.
"They will give you guidance on when to service and what to look for," she said.
Keeping detailed records
Documentation of equipment maintenance is an area where most dental practices need to do better, Hunter said.
"When we think about documentation, we tend to think of patient chart notes, but there is some serious documentation that needs to happen in relation to OSHA [the U.S. Occupational Safety and Health Administration], infection control procedures, HIPAA, and, not to mention, general office maintenance," she said.
Hunter added that there is so much misinformation, including whether spore testing needs to be done, among dental teams.
"Someone told them at one point it wasn't necessary anymore, and they believed it," she said. "So they just stopped doing it (mandatory spore testing). Waterline maintenance is another area that offices truly have no clue about when it comes to how to treat, shock, and test their water."
Hunter said that some individuals she has spoken with have claimed that waterline maintenance isn't necessary because they use the best source of water available. However, that's not true, she said.
"Education is a powerful tool," Hunter said. "Once I am able to educate them, they get it. Getting offices to that point is difficult because not every office does the required yearly training."
Speaking of training, every office must maintain annual training records for their teams, and new hires must be trained within 10 days of employment. In fact, it is one of the first things that a state dental board, OSHA, or HIPAA will ask for if they visit, Hunter said.
Additionally, with such an influx of new hires at practices, many of them know little about general maintenance, she said.
"We are so busy trying to train them in other areas that this has really fallen off the wagon," Hunter said. "I will say that you are only as good as the person who trained you, so if that person doesn't take maintenance seriously, then they won't reinforce that when it comes to training new hires, so the ball really gets dropped."
To stay on top of maintenance, she suggests creating a calendar that breaks down all of the maintenance duties and when they need to be done each month. The calendar should be hung in the sterilization room or lab so it is seen regularly.
As part of this calendar, repairs to equipment should be noted as well. For example, if a handpiece was sent out for a turbine change, the date it was returned, its serial number, and the date it was placed back in service should be added to the calendar or logbook. If a month later a handpiece goes out, the serial number can be checked to see if it's the same one that had been previously serviced.
"If so, it may be under warranty, and you can send it back in at no cost," Hunter said. "If you aren't keeping track of the serial numbers, you could be paying to repair the same handpiece over and over again. It could be an aftermarket turbine that is being used and isn't holding up."
Maintenance is not a one-person job
Sometimes, only one person oversees maintenance and, Hunter said, that sets offices up for failure. The person in charge becomes overwhelmed and must leave some of their duties to be done another day and those tasks are often maintenance. Offices also get behind on maintenance when the person keeping track of it gets sicks or leaves the job, she said.
"(Then) you are stuck with a team who does not know how to do any of that," Hunter said. "They are at a loss and have no clue how to jump in and handle it. Don't do that to yourself!"