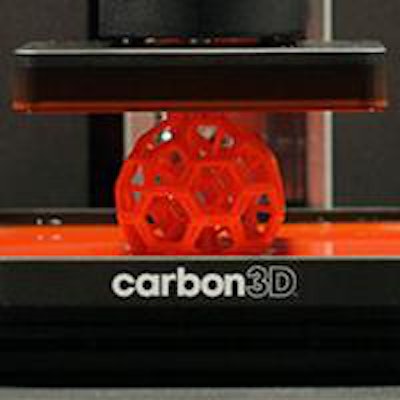
Do you remember in "Terminator 2: Judgment Day" when Arnold Schwarzenegger's character points a gun at his nemesis robot, T-1000, and says, "Hasta la vista, baby"? Schwarzenegger blasts the robot apart, but T-1000's melted pieces reassemble and he rises up, rebuilt, from the liquid base.
Carbon3D's new technology wants to do just that -- but with dental structures.
Joseph DeSimone is the CEO and co-founder of Carbon3D, a company with an innovative approach to polymer-based 3D printing. DeSimone recently took the Redwood City, CA, company and its new technology out of stealth mode by simultaneously announcing its 3D printing method at TED2015 and through a feature story in Science magazine.
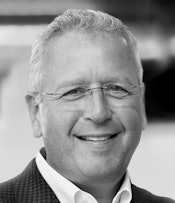
"We were inspired by the 'Terminator 2' scene for T-1000, and thought, 'Why couldn't a 3D printer operate in this fashion?' ... where you have an object arise out of a puddle in real time with essentially no waste to make a great object," he said in the TED talk.
Right now, two 3D printing approaches are commonly used. With the first, an additive method, a printer deposits material layer by layer to build the object. With the second, a milling method, machines carve a new object from a block of material, which is already used in dental offices to print some restoratives.
Carbon3D's approach differs from the existing approaches in that an object literally arises out of a puddle in real-time using continuous liquid interface production (CLIP). This process harnesses ultraviolet (UV) light and oxygen to continuously grow objects from a pool of resin.
The process works like setting a composite
Photopolymerization is used to create layerless 3D-printed objects. A pool of resin rests on a transparent window that is permeable to oxygen, like a contact lens. By controlling the amount of oxygen that can get through the window, CLIP creates a micro-sized "dead zone" in the resin pool where the photopolymerization cannot occur.
The device projects cross-sectional images of a 3D model from underneath the glass into the dead zone. By controlling both the UV light and oxygen, the printer can control how the physical object cures, somewhat like when setting composites. This type of printing occurs in three dimensions at once, and an object continuously emerges once it breaches the dead zone. (See the images below or watch a YouTube video of the process.)
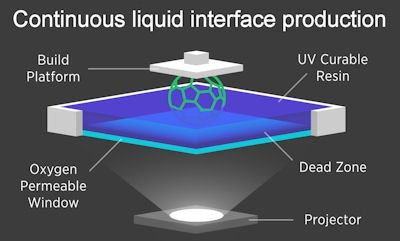
CLIP is up to 100 times faster than additive 3D printing, and its objects are stronger, because they are not assembled in a thin layer-by-layer fashion, according to Carbon3D. CLIP also works with a wider range of materials than other, traditional polymer printers.
CLIP has potential for dentistry
The ability to quickly create complex materials is especially relevant to dentistry. While some dentists already create crowns using 3D printing and other restoratives using milling, they cannot create more complex pieces with detailed parts inside and outside of a single structure.
It is foreseeable that one day practitioners can design and print incredibly detailed dental structures using CLIP all while their patient is chairside.
"Think about if you need a stent in an emergency situation. ... Having a stent that's designed for you, for your own anatomy with your own tributaries, printed in an emergency situation in real-time ... [is] really game-changing," DeSimone said in his talk. "Or digital dentistry, and making these kind of structures even while [the patient] is in the chair."
Carbon3D's printer is still in development, but the company has raised $41 million so far to commercialize the technology.
"If 3D printing hopes to break out of the prototyping niche it has been trapped in for decades, we need to find a disruptive technology that attacks the problem from a fresh perspective and addresses 3D printing's fundamental weaknesses," stated Jim Goetz, Carbon3D board member and a partner at Sequoia Capital, which led the company's Series A funding, in a press release.